本发明涉及乳化重油产品的生产工艺,具体地说是一种在输送温度条件下乳化重油产品的生产工艺.
重油乳化技术在国内外开发应用已有十几年的历史,一些高能耗电器业为降低燃料消耗和生产成本相继采用该技术,但因生产技术设备落后(罐式800C以上温度搅拌)、乳化剂质差价高并且添加量大(1-3%)造成生产成本较高,混合效果差,成品不易储存,只能为间断式批量生产的直接配燃燃料。
根据我国的能源结构调整和乳化重油产品发展的需要,从节能和环保两个方面出发,我们研究了乳化重油工业化生产及仓储技术专利,使乳化重油想产业化发展成为现实,但是技术存在的以下缺陷影响了产品质量的进一步提高。
A、
重油和水必须加热至500C以上的温度乳化,尤其重油的加热时间长,燃料消耗大,增加了生产成本,同时对不具备重油加热条件的油库而言是难于克服的困难,
B、
水乳液配剂时间长,乳剂用量偏大(0.8-1%),生产成本相对较高。
C、
重油和乳化水的预热器为被动式,预混状态为粗线形,制约了后级剪切混合的均匀效果。
D、
乳化关键设备为高剪切乳化机,采用被动式压力流量乳化条件控制,由于受到重油温度、粘度变化的影响,造成乳化的波动和产品质量的变化,因此生产操作难度大,关键部位易发生扭曲和疲劳断裂。
E、
产品的显微观察,水颗粒直径1-2um占85%,5-10un占15%,若以质量对比测算,5-10um的质量比达40%以上,该项指标是乳化重油产品稳定性能和燃烧性能的关键。
本技术的目的就是解决上述问题,而提供一种在储存输送温度条件下乳化重油产品的生产工艺。
在输送温度条件下乳化重油产品的生产工艺,其特征在于:
一、
按照乳化重油产品的确定条件,将一定数量的乳化剂与150倍-200倍的一定温度的淡水竟搅拌和混合条件的充分稀释,配制成水乳液。
二、
经管道自流的重油与泵送水乳液按比例连续输入,通过预乳化混合器进行大流量、连续式的强制性混合,将重油中的胶质或沥青形成的紧密性胶团打碎和分解,使重油与水乳液得到有效混合,形成油包水的基本状态。
三、
预混合后的油乳液再经油泵吸入增压,并计入精细高剪切混合器被切向和纵向等距离高速切磨后,使水颗粒呈大小均匀并分散于重油之中的油包水的稳定状态,即成为乳化重油产品,输入成品油罐储存。
本技术适用于不同规格品种重油的常温生产(储存输送温度)以及与重油相同工艺条件的应用,起完整的工业连续化生产设备、工艺技术和专用乳化剂,使乳化重油产品的产业化发展成为现实。
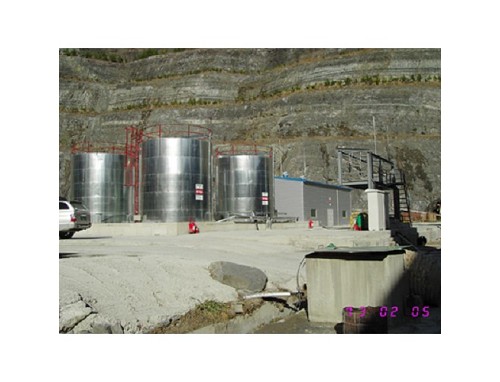
关键词 高剪切乳化机 静态混合器
|